The nature and severity of damage suffered by stern tube / shafting systems, vary greatly – ranging from a simple aft seals’ leakage that can be rectified over a few days whilst afloat, to loss of propulsion involving costly salvage operations and extended repairs in drydock.
In the past, damage to a stern tube was often considered a relatively straightforward casualty by surveyors. The cause was often obvious – contact with a floating object such as ice, fishing nets or ropes, for example.
These causes still exist of course, but the significant increase in frequency over the past years, without any apparent explanation, raises concern.
A new “thorn” for owners and insurers
Over the last decade, the number of shaft / stern tube-related claims Gard has handled, either as claims’ lead or on follow accounts, exceeds 700 with the below spread over the years:
Total stern tube-related claims in Gard in excess of USD 5,000
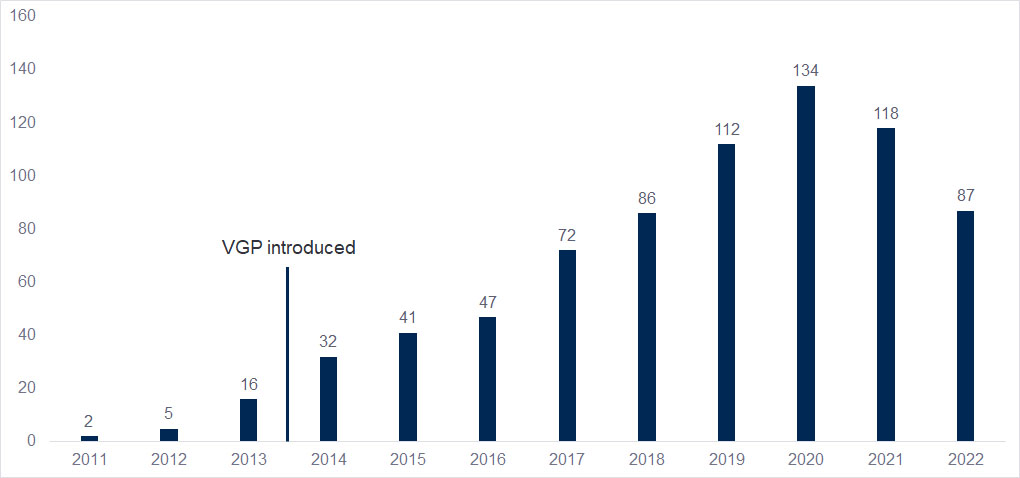
Source: Gard
To be clear, over this same period of time, the number of vessels insured with Gard has also increased. So, is the increasing number of claims just reflecting the higher number of vessels insured? No. Even when taking into account the total number of vessels covered, we still see that the share of stern tube-related damages is increasing (see chart below).
So, what is happening?
Frequency of the stern tube-related claims in Gard in excess of USD 5,000
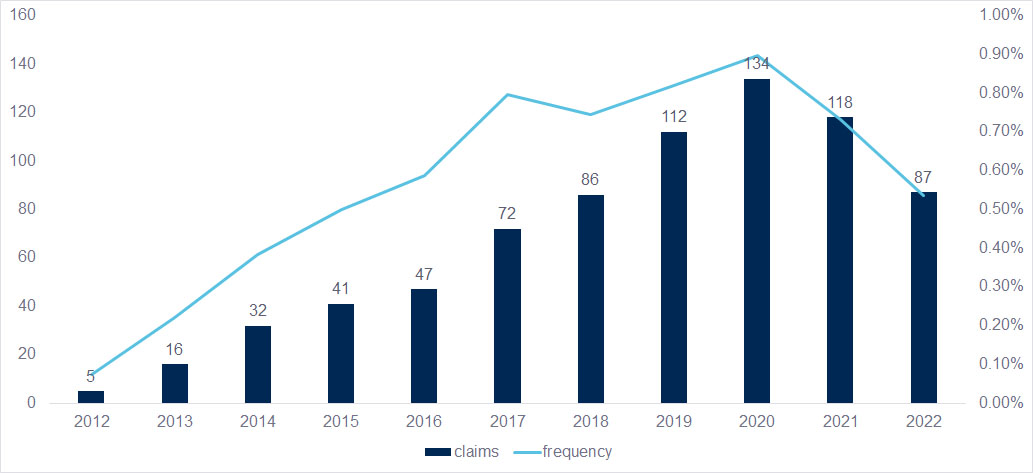
The use of Environmentally Acceptable Lubricants
As shown in the first bar graph, the significant increase in claims seems to have followed the introduction of the revised Vessel General Permit (VGP) requirements in 2013 by the U.S. Environment Protection Agency (EPA). These require all vessels over 79 feet trading in U.S. waters to use Environmentally Acceptable Lubricants (EALs) in all oil-to-water interfaces.
According to a study performed in 2019 by DNV GL with the assistance of Scandinavian Insurers (Gard, Skuld, Swedish Club & Norwegian Hull Club) it was discovered that two key features of EALs make them different from the traditional mineral oils widely used before VGP requirements came into force:
·Pressure / viscosity coefficient => under high load operations (i.e. hard turns at high speeds) the EALs operate with a lower safety margin of the minimum oil film between the tailshaft and the bearings
·Viscosity index (EALs significantly higher than mineral oils) => EALs operate with lower viscosity under lower temperatures (i.e. mooring trials and cold start-up)
Damage caused due to the above characteristics can be prevented to some extent by either using EALs with higher viscosity (one grade up) or by modifying the aft bearing design to smoothen / increase the contact surface between the bearing and tailshaft by double slope design instead of single.
In addition, another notable characteristic of the EALs is poor hydrolysis stability when interacting with sea water once bypassing the aft seals. When contaminated with sea water, lubricant decomposes, and carboxylic acid is generated which can damage the seals resulting in even greater sea water ingress.
The speed of hydrolysis depends on various factors, for example, chemistry of the oil, temperature and additives. The most important factor, however, is the quantity of sea water present in the lubricant. According to IACS, the upper water limit suggested is 1%, which is the same for both the traditional mineral oils and EALs. Experience has nevertheless shown that this limit is quite “relaxed” and somehow misguiding when it comes to EALs, as apparently even minor water quantities can trigger the hydrolysis reaction of the EAL and affect its characteristics including stability.
In sum, it has been confirmed that the performance capacity of the traditional mineral oil – the strong lubricating oil film, consistency at the presence of water in the oil and excellent seal compatibility – cannot be matched by the EALs. This is why Shipowners tend to go back to the “traditional” mineral oils combined with air-type seals, for both newbuildings and existing vessels.
New root cause analysis
In Gard, we have conducted an internal investigation of all the stern tube damage cases we encountered in the previous 10 years (from 2013-2022), in an attempt to identify any patterns with respect to causation.
It was evident from the start that the type of vessels that suffer most from such damages are Bulk and Container Carriers, accounting for 53% of the occurrences. In total, these segments make up 44% of Gard’s Hull and Machinery portfolio (see pie chart below).
Stern tube-related claims in Gard, by vessel segment
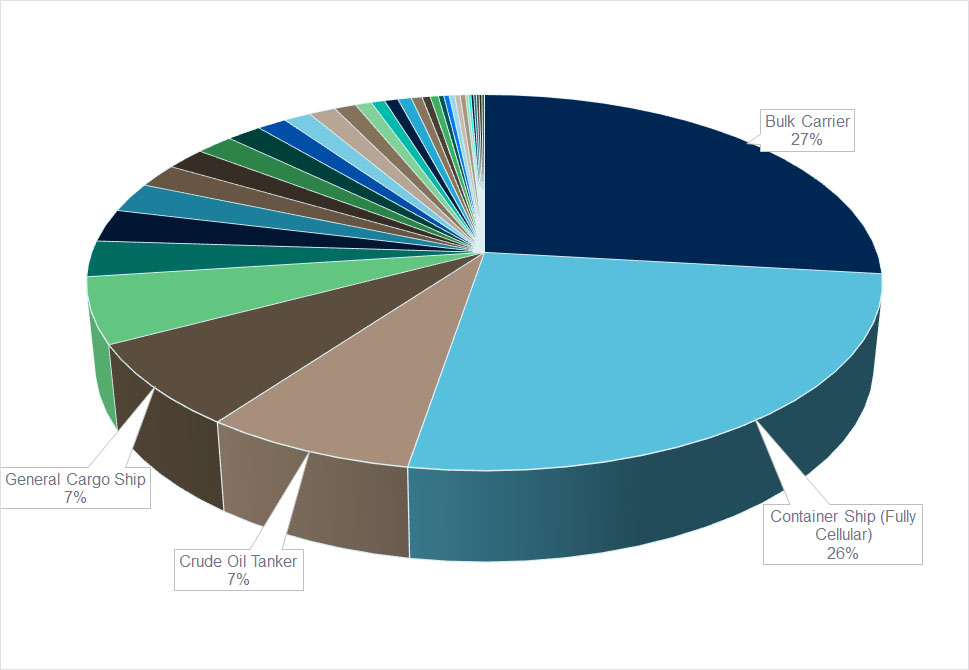
The root cause investigation was thus narrowed down to focus on Bulk and Container Carriers, with the reported causes categorized as follows:
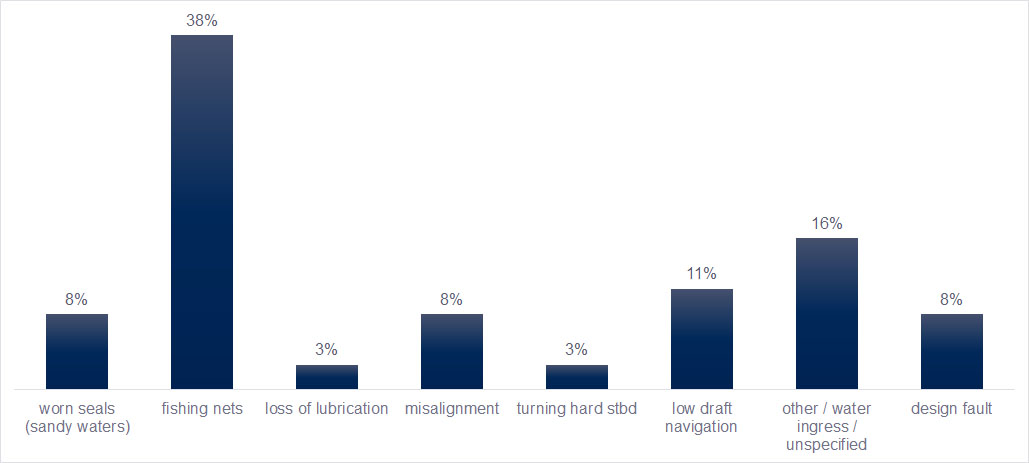
As seen above, a large number of the incidents were attributed by the surveyors to fishnet/ropes entering the stern tube seal area causing seawater to contaminate the stern tube oil and accounting for 38% of the cases. Indeed some 500,000 – 1 million tons of fishing gear is lost or abandoned at sea every year, according to World Wildlife Fund (WWF).
However, we believe that the “fishing nets causation” may have been overrepresented as the main explanation, leaving little room for further investigation into other possible factors.
In fact, many of the stern tube bearing failures since 2014 did not seem to involve any contribution from external factors (i.e. contact marks on propeller blades, nets’ entanglement in the aft seals’ system, groundings etc.).
80 per cent of cases involved EALs
Interestingly, our analysis show that as many as 80% of the incidents investigated, involved stern tube seals’ failure with EAL oil in use whilst the average age of the vessels was 12 years.
“Design fault” was also an interesting category, which has nevertheless not been fully explored. It appears that other than some misalignment problems due to error in design from the Shipyard (resulting in damaged bearings), other factors greatly affect the lifetime and condition of the tailshaft assembly such as:
·Single stern tube bearing design (increasing risks)
·Improper monitoring of aft seal lub oil (no design for obtaining representative oil samples, no circulation of the oil)
·Bearings tolerances as thoroughly studied by DNV
Other than the above and despite the fact that same were not presented in any of the survey reports we reviewed, we have concluded that several additional factors play a significant role either in the initiation of damage or in the aggravation of damage, such as:
·Crew awareness and monitoring procedures (especially regarding the presence of water in the EAL)
·Allowable % of water as per IACS suggested limits which do not fully take into consideration the certain types of EAL oils that are prone to give accelerated wear of seals (due to EAL hydrolysis especially for emulsifying EAL based on unsaturated esters)
·Mixing of EALs with mineral oil during topping up of the aft seal tank
·Sailing for prolonged time with partly immersed propeller. Heavier propeller / larger diameter / lower rpms
Selection of EAL type (base oil)
·Improper past repairs (i.e. seals’ bonding)
·Use of non-original / after-market seals
Advice to shipowners
To prevent or mitigate stern tube damage, we recommend that Owners take the following actions.
During Vessel‘’s operation
·Selection of proper EAL viscosity (one grade up) and thoroughly consider the various qualities of EAL being offered in the market to ensure minimum risk of failure (i.e. selection of EAL based on fully saturated synthetic esters, non-emulsifying)
·Frequent testing of representative oil samples from aft / fwd seals’ tanks and stern tube system
·Retrofit installation of filtering / surveillance systems available in the market
·Continuous monitoring of bearings’ temperature
·Close monitoring of aft seal oil circulation if such a system is fitted.
·Frequent monitoring of the drain tank in case air-type seals are used
·Change of aft seals’ oil once sea water presence has been confirmed even for minor quantities. Drain water if non-emulsifying EAL is used and water contamination was swiftly spotted.
·Keep a close eye of elevated levels or increasing trend of water content, TAN, bearing / shaft material elements (Tin, Lead etc.) in the lub oil analysis
·Avoid continuous sailing with partially immersed propeller (if unavoidable, propeller to be used with reduced rpm)
·Properly check condition of rope guard and net cutter during UW surveys
During routine repairs / new buildings
·Air-type seals are preferred together with use of traditional mineral oil
·Modify aft seal oil system to the continuous circulation type rather than the static / gravity type. Note some stern tube seals manufacturers have reduced the provided warranty from 5 to 2.5 years for single piping s/t lub oil arrangements for EAL oil
·Use of multi-sloped bearings’ modification at first opportunity in dry dock to ensure better hydrodynamic lubrication between bearings and tailshaft
·Verification of shaft alignment from M/E flange to aft end via laser & jack load tests
·If not already fitted, consider installing net pickup ring and rope cutter to avoid ropes/fishing net to enter the stern tube seal area.
Source:
Gard
The opinions expressed herein are the author's and not necessarily those of The Xinde Marine News.
Please Contact Us at:
media@xindemarine.com
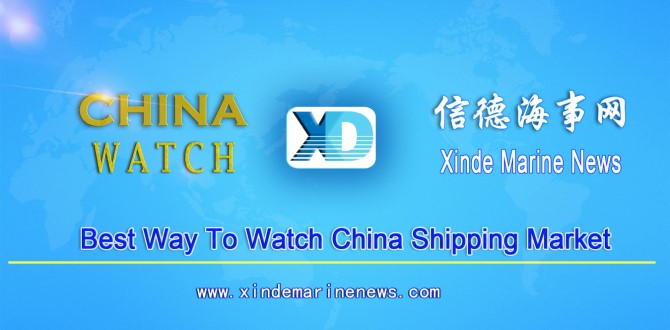